Increasing lighting efficiency can make a big difference to running costs. This is one of the reasons driving the move to replace traditional lighting solutions with LEDs in recent years.
2022 Top Article - Indoor Agriculture: Driving up LED Efficiency to Reduce the Costs of Artificial Sun
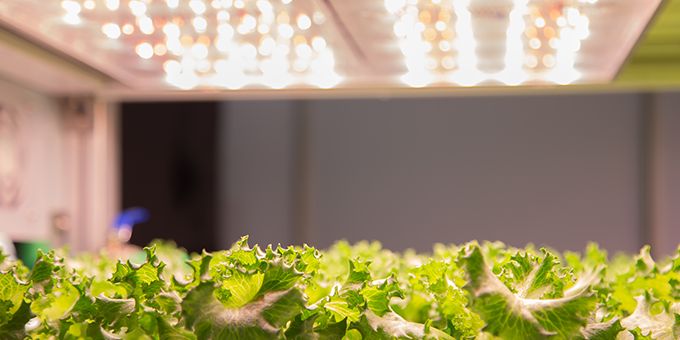
Joe Voyles, Vice President, Industrial | Advanced Energy Industries, Inc.
Indoor horticulture or Controlled Environment Agriculture (CEA) enables increased yields and more predictable all-year-round growing conditions, allowing crops to be grown closer to where they are to be consumed. Driven in part by growing consumer awareness of the benefits of consuming fresh, locally produced food, this market is predicted to expand at a compound annual growth rate (CAGR) of 10.9% from 2021 to reach a value of over $75 billion1 by 2028. The cost of lighting large indoor areas is leading growers to choose more efficient and more controllable LEDs over conventional lighting systems. However, running costs remain high. Here we consider a new system for powering LEDs that significantly improves efficiency to drive down electricity costs.
Energy costs are a key issue for indoor growers, frequently second only to labor costs. Controlling and reducing electricity is critically important to both commercial feasibility and meeting sustainability targets. When we consider that lighting is one of the biggest consumers of electricity in an indoor growing environment, increasing lighting efficiency can make a big difference to running costs. This is one of the reasons driving the move to replace traditional lighting solutions with LEDs in recent years.
LED lighting in horticulture
LEDs offer longer lifetime, lower energy consumption and lower maintenance costs than traditional horticultural lighting options. They also offer deliver greater control over the light output across different wavelengths. This allows growers to more closely match spectra to the needs of their plants. In addition, luminosity can be adjusted to manage production depending on plant species and growth stage. The availability of smaller LED lights improves control over where the light goes, increasing efficiency and reducing energy consumption.
Greater efficiency means that LED lights operate cooler than traditional high pressure sodium (HPS) bulbs so they can be placed closer to plants, resulting in increased farming density. Less heat also lowers water consumption, thereby reducing cost. So far, the primary adopters of horticultural LED lighting have been traditional greenhouses where it is used to supplement natural light. However, when used in larger greenhouses (‘growing warehouses’), LED lighting can improve control over the nutrient balance and growth cycle of a wide range of crops.
Greenhouses are generally lit from above, illuminating the hall and plants from the ceiling level. Typically, installations would involve fitting LED luminaires in place of HPS lamps, modifying the spectral content of the light. While this approach generally works well, there are some challenges including light being concentrated on certain plants, ensuring uniformity and constant quality of the light spectrum, as well as the generally significant amount of electrical power consumed.
Vertical farming places the lighting much closer to the plants but continues to illuminate from above. The layout brings additional challenges including heat (due to proximity and plants shading each other. The need for uniformity and constant quality of the light spectrum remain a challenge in vertical farming.
Intra-canopy lighting involves lighting from the side or even in-between plants. HPS lighting was too hot for this approach, but more efficient LED lighting now makes it possible. The directionality of light can be a challenge with this approach and, as with lighting from above, growers must ensure uniformity and constant quality of the light spectrum.
Improving the Efficiency of CEA Lighting
Despite the inherent efficiencies of LEDs over their conventional counterparts, the sheer volume of high-power LEDs still makes electricity consumption in lighting a dominant cost for growers. At present, around 100 watts of LED power is needed per square meter and lamps operate between 12 to 18 hours a day. While the exact power requirement depends on a number of factors, including the crop being grown, the power usage from these LEDs can account for well over 50% of the total electricity bill.
Costs can also increase due to the way in which the energy is taken from the grid. When current and voltage are not in phase, for example, an additional load can be placed on the supply. Known by engineers as Power Factor (PF), this load does no useful work in powering the lighting but is metered, thereby increasing the costs. Then there is Total Harmonic Distortion (THD), which is a measure of how much of the distortion of a voltage or current is due to ‘harmonics’ in the signal. A lower THD typically means higher power factor, lower peak currents and higher efficiency – all of which are desirable in a power system and beneficial to the application. While these issues may seem removed from the day-to-day running of a CEA facility, many utility companies now use smart meters for large energy users to measure THD and modify billings accordingly.
It is with these factors in mind that Advanced Energy has developed a new approach for powering LED lighting in the horticultural sector.
The challenge with conventional approaches to LED lighting is that the power conversion circuitry supporting the LED luminaires has inherent inefficiencies. While LED drivers may achieve power conversion efficiencies in excess of 90%, converting the power individually for each lamp rather than in one go results in a lower PF and a higher THD.
Furthermore, with traditional designs, the fixtures operate from a single-phase supply. Without careful planning, this can lead to imbalances on the three-phase supplies that typically feed the growing facilities. All of this results in less efficient and more expensive electricity use, even before considering any levies that the utility company may impose for causing poor power quality on power feeds.
Figure 1: An improved approach to CEA lighting power conversion
Figure 1 illustrates an improved approach to LED lighting that improves energy savings by as much as 12%. In this system, power is provided via a three-phase power conversion subsystem in a control room outside the growing area. The subsystem, which is driven by Advanced Energy’s Artesyn iHP family of scalable AC-DC power supplies, provides a single point of power conversion that distributes DC power, rather than AC, directly to the individual LED lamps. The resulting high PF and low, grid-friendly, THD signature improve efficiency.
In addition, no matter how efficiently they operate, all LED drivers give off heat. If we assume a power rating of 30 W per driver, a typical driver efficiency of 95% and around 1800 LED lights per acre, then a significant 2,700 W (9212 BTU/hr) per acre will be dissipated as heat. In the past, growers have employed air conditioning and other cooling solutions to remove the heat from the grow environment. Now, by doing away with individual drivers, the monolithic remote DC power solution minimizes the need – and, therefore, reduces the energy required – for cooling. Depending on installation, these further savings can contribute to reductions in HVAC electricity requirements by up to 5%.
A practical implementation
Figure 2 shows an example lighting configuration that uses a balanced 3-phase (347 / 600 VAC) supply with a centralized power conversion outside the growing area that reduces cooling costs.
Figure 2: Example lighting configuration using a single 3000 W iHP power module
Precise control can be delivered either via an analog control voltage which could be an automated system, or a simple dimmer switch. In more sophisticated set-ups, connection to a network allows remote control from anywhere.
By distributing 250 V, losses in the wiring are significantly reduced over lower voltage configurations, which saves cost. This also permits the use of thinner wire, further saving costs and weight. Additionally, as the luminaires are arranged in a parallel configuration, the failure of one will have no impact on the rest of the system, unlike serial configurations where a single failure can take the entire system down.
Figure 3: Cost comparison of CEA system approaches
Figure 3 shows the cost comparison of various lighting models, taking into account installation and operating costs.
While the installation cost associated with direct integrated lighting is reasonable, the cost of the 240 integrated power converters is very high. In addition, as power conversion is performed in the temperature-controlled area, there is also a significant ongoing cost for additional cooling.
Moving to a 48 V distributed system with power conversion performed separately outside the controlled area moves the bulk of the cost to the wiring while significantly reducing the cost of power conversion. Because all cooling costs are eliminated, this approach shows a 10% saving.
If the approach from Figure 2 is implemented, then the cost of the power supply is the same and there are no cooling costs. However, the wiring costs dramatically reduce to around one-fifth of the previous approach, meaning that the overall cost of this approach is less than 40% of the cost of the 48 V system.
References:
The content & opinions in this article are the author’s and do not necessarily represent the views of AgriTechTomorrow
Comments (0)
This post does not have any comments. Be the first to leave a comment below.
Featured Product
